Revealing the Significance and Practicality of “Bulk Purchase” in Reducing Construction Cost
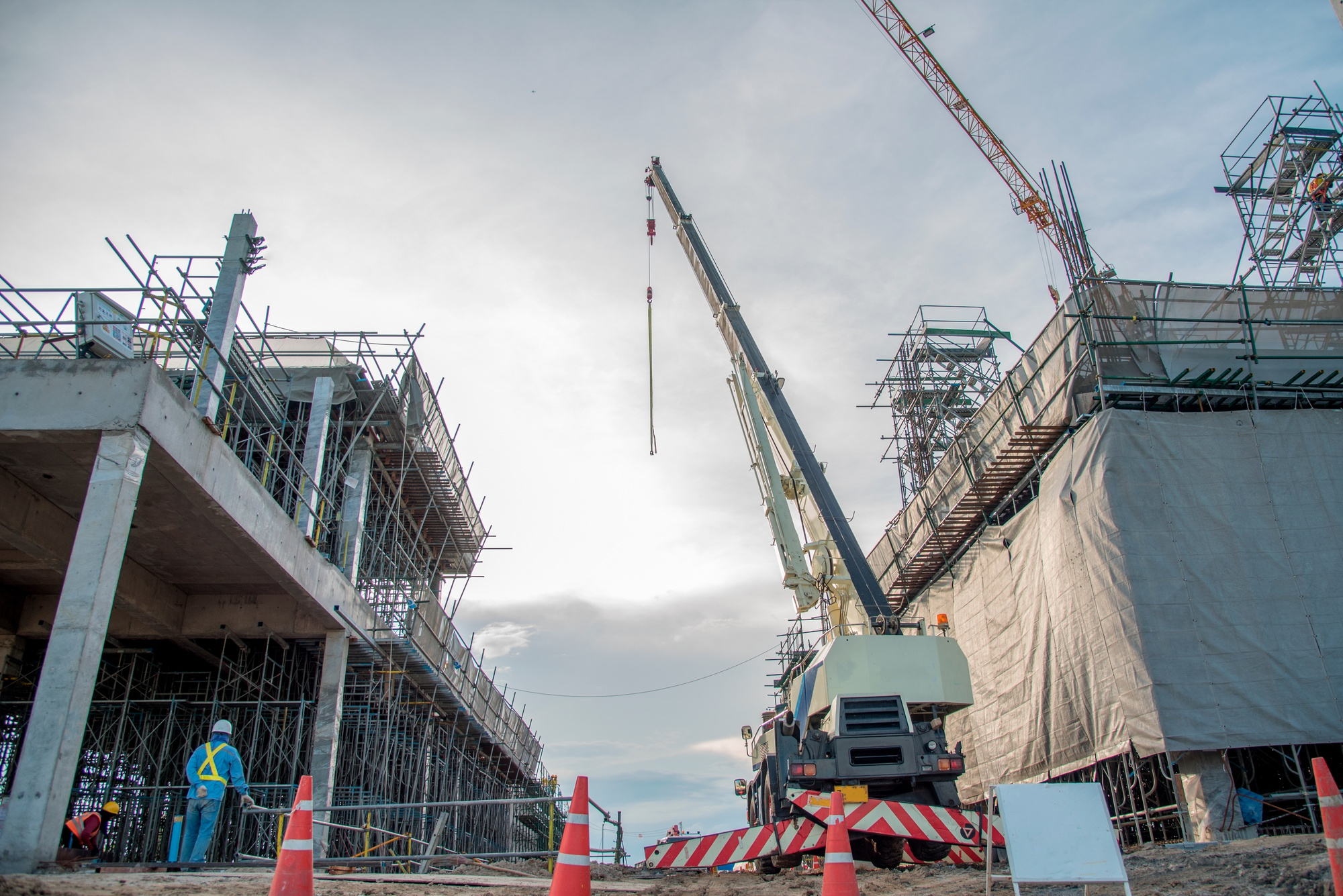
According to a report by Turner & Townsend, Malaysia’s construction tender prices are expected to grow by 3% in 2024, which is a softening of two percentage points compared to the previous year. This seems to be a positive shift as the pace of construction cost escalation are moderating, while issues such as manufacturing backlogs, logistics, and supply chain disruptions are gradually stabilising.
However, an improvement in the property sector dynamics indicated by the pick-up in property transaction activities, reduce in overhang and unsold units, and recovery in new launches; will soon to spice up the outlook for the construction sector. As the construction industry starts to regain its momentum across all sub-sectors (Figure 1); coupled with the potential rollout of big-ticket infrastructure projects, and persistent factors that contribute towards higher cost of doing business such as rising inflation and elevated freight costs; building material costs are sure to increase, with no sign that prices will fall to pre-pandemic levels. According to the REHDA’s survey, construction costs are expected to increase by an average of 15% in the first half of 2024.
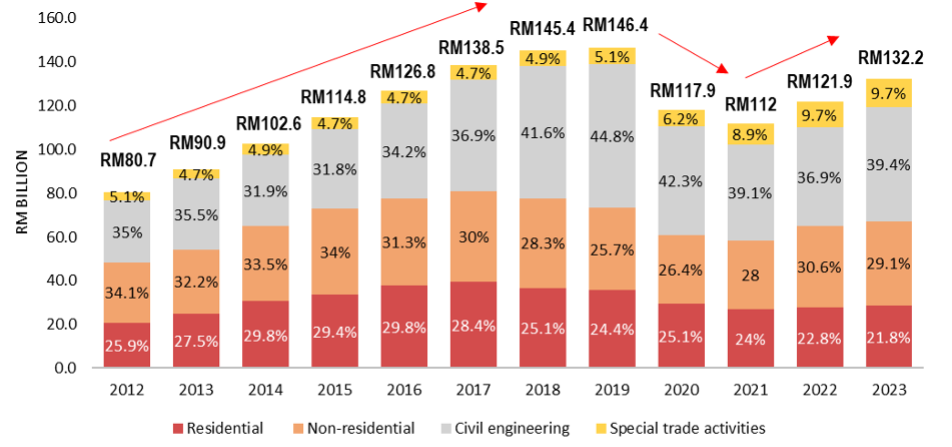
Source: DOSM
Figure 1: Value of construction work done by sub-sector, 2012 – 2023
While it is not uncommon that any risk associated with price uncertainty will eventually be passed on to the end users, property developers are caution about price increases of their products, as they may have to bear with a tougher business operating environment. Unless the soaring is too high and there is no way to curb the increased price tag, developers tend to offset the increase with strategic material procurement and smarter spending processes, to ensure the final prices for potential homebuyers are affected as minimum as possible.
Purchasing building materials in bulk is a viable strategy to reduce construction costs, as high-volume purchases are not only beneficial in cost saving for developers who have multiple ongoing projects with the same product requirements, but also contributes towards fewer man-hours wasted on-site due to repetitive material loading-and unloading processes, thereby helps minimising lead time issue. Besides, bulk purchases can also guarantee project consistency in terms of material supply, product quality, and working efficiency, which then enable developers to stay ahead of their competition.
Nevertheless, bulk purchase may not be a suitable strategy for all developers in the market. This is because, for bulk purchases to pay off, contractors need to have an opportunity to influence specifications. Only when contractors have a voice in design and have a sizeable backlog, then bulk purchases are a way to save big in the long run. More importantly, the same contractor has to involve in multiple projects that share the same specifications and similar design so that materials purchased in bulk can be utilized across these projects.
Unfortunately, the Malaysian property developers are a diverse bunch. Not all of them are contractor-turned developers or running their own construction arm that can harness the long-term savings from bulk purchases. In common industrial practice, property developers, especially those “pure developers” who are the project owners but do not carry out the construction works, will tender out their projects with specifications and design done by the consultants (architects and engineers) they engaged in the planning stage. Contractors only come into play at a later stage when the project details are confirmed, which causes them to have less say in building materials procurement.
While a “pure developer” may have several construction projects running simultaneously, he/she may not necessarily engage the same contractor for all the projects, because these projects could vary differently in terms of location, selling prices, development concepts, and target markets, which pose challenges to standardization. Likewise, a contractor may serve different “clients” that require different project specifications. These further limits the possibility for developers to pay upfront to purchase in bulk to avoid wasted inventory. More importantly, what concerned the most is that pure developers may not necessarily enjoy a significant cost reduction by bulk purchasing, given that not all building materials can be purchased in bulk from the common industrial perspective.
As shown in Figure 2, iron & steel materials and cement & concrete materials are the two-most utilised materials in construction projects, account for more than 50 percent of the total building material costs for both the residential building and non-residential building projects. In principle, bulk purchases for both the cement and steel could help reduce construction cost substantially, but this is rarely carried out in practice due to two major constraints.
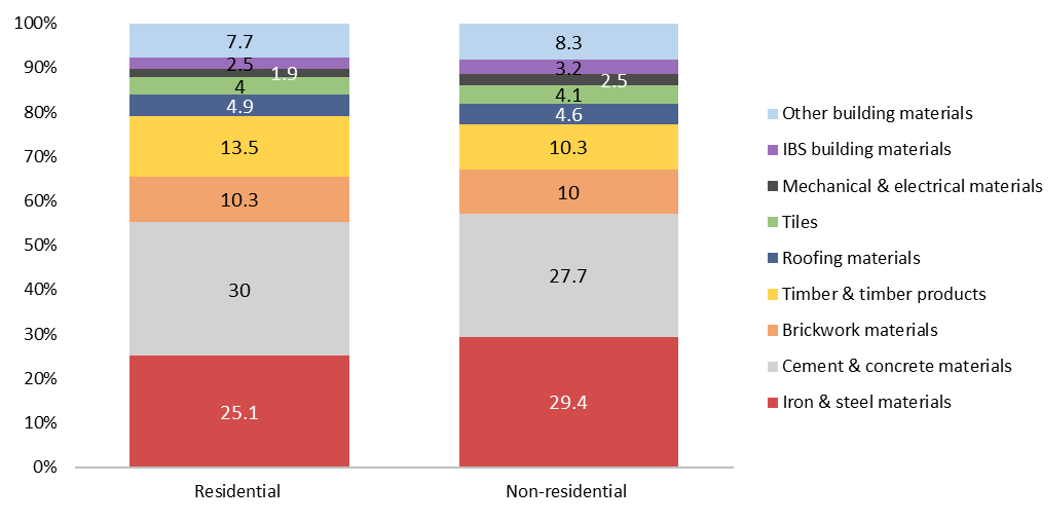
Source: DOSM
Figure 2: Breakdown of building material cost (%) in residential and non-residential projects
Cement (both bagged and bulk) is a perishable material and its life span very much subjects to humidity and temperature under which the cement has been stored. If correctly-stored, unopened bags might have a shelf life of up to six months at best. Aside, it is always recommended to use fresh cement for all structural jobs (i.e. jobs that require maximum strength).
For bulk purchase of cement, it could be explored locally and globally. The challenge greatly encountered for bulk cement purchased from oversea by developers or contractors. Presently, only cement manufacturers own the cement terminal at major ports, such as Pasir Gudang, Westport, Miri, and Sibu, which have the infrastructure and equipment in handling the bulk cement import. To own this facility, size and scale do matter, because one must be sizable enough to have financial muscle in capex as well as significant volume of handling to make this avenue economically viable. To aggregate the bulk purchase volume from all the projects concurrent running (of same developer) or from a handful of developers and contractors would be a great testament to the coordination for cement distribution within the best use life span.
Meanwhile, for steel materials, particularly long steel, the bulk purchase from local mill generally could not garnered a fixed term supply (for entire project duration) from local millers given that long steel is susceptible to price fluctuation. This simply leave developers and contractors to the option of bulk purchase from overseas. The key apprehension of long steel would be the corrosion and the corrosion rate imperilled by type of metal, the exposed environment and presence of any protective coatings.
Long steel also varies in sizes for ribbed bar (i.e. Y10, Y12, Y16, Y20, Y25, Y32 and Y40) and round bar (R6, R8 and R10). To have the right sizes at the same time the right quantity would somehow not be impossible. But, to have the long steel distribution over the total project duration, one needs to have considerable warehouse space with sound financial. Chiefly, cash upfront is obligatory upon booking while balance payment upon ready for delivering from original port.
Often, cost savings from bulk purchases are computed against the fixed contract rate instead of the real market rate; and this bulk purchase is merely rate pegging. With significant cashflow earmarked for the bulk purchase, the perceived savings whether outweighs the cost would be questionable when long steel rate plummeting given that developers and contractors could not discount the possibility of local millers upon reacting to domestic oversupply or global supply dynamics.
Accordingly, global long steel price always being benchmark against domestic long steel price. The difference between the two prices is price spread (price disparity). Whenever there is an emergence of wider price spread of global long steel price and domestic long steel price, a window of opportunity is open to steel dealers for maximising their profit margin by importing in long steel before the next price correction. Developers and contractors could always ride on this wave of price moderation by adjusting their project progress to capitalise on their “right price” (on or below fixed contract rate) effortlessly without additional financial burden.
In common industrial practice, only PC rate items are often listed for bulk purchases. PC stands for prime cost, which is an amount of money that has been allowed for an item in the project for which the labor that goes with the item has been included within the total price of the project. PC rate items normally include architectural finishes such as tiles, sanitary wares & fittings, faceplates, ironmongery, fire rated door, timber door, door frame, distribution board etc., which are selected by the architect or the project owner in advance, with costs locked in before signing the contract with contractors so that the whole project cost is known before it even commences.
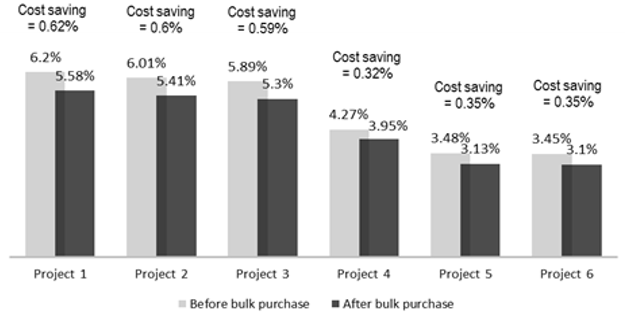
Figure 3: Cost of PC rate items as a percentage of total construction cost and savings via bulk purchases of PC rate items
However, PC rate items only account for a small portion of the total building material costs, in which their contribution towards the reduction of construction cost via bulk purchases is insignificantly. For example, six construction projects located in Klang Valley region were studied, and the initial costs incurred by PC rate items before bulk purchases carried out found range from 3.5% to 6.2% of the total construction costs (TCC) (Figure 3).
Assuming standardization in specifications could be done to all projects, and these projects were using the same PC rate items to facilitate buying in bulk. Reduction in construction costs was observed across all projects, but the impact of cost saving via bulk purchase of PC rate items was smaller than expected. For instance, in Project 1, PC rate item costs were initially accounted for 6.2% of the total construction costs, and have been reduced to 5.58% through bulk purchases, resulting a saving of 0.62% of the project’s construction costs.
Apparently, the impacts of cost saving through bulk purchases of building materials are not as significantly as one perceived. Should a developer wish his/her products to be more price-competitive in the market, value engineering is an essential construction process to be undertaken. In principle, value engineering is the review of new or existing products during the design phase to reduce costs without significant compromise on quality or function of the product. In construction, value engineering is a prescriptive process for analyzing project components – such as materials, systems, equipment, or features – to find alternatives that produce the same results but provide greater value and lower costs.
While value engineering is all about making the best use of the available budget, it is important to note that value engineering is not a knee-jerk reaction to avoid going over budget. The objective of value engineering is not to trim the bottom line, but to maximize function at the lowest possible cost. The ultimate goal of conducting such exercise is to ensure that the owner is not over-paying for quality when an equally effective, less expensive option exists. Doing so requires know-how, teamwork and reliable construction cost data. This certainly requires a multi-party-collaboration from developers, contractors, and design professionals during the design stage of the project.
A typical example of value engineering exercise that is widely used is by adopting post-tensioned system to the transfer slabs for high-rise buildings. To note, many transfer slabs constructed in the past were heavier and thicker. With the adoption of post-tensioned system, the concrete thickness, weight, and reinforcement can be reduced substantially, while at the same time increasing floor-to-floor headroom, as well as enhancing crack resistance. Most importantly, it is more cost-effective after all.
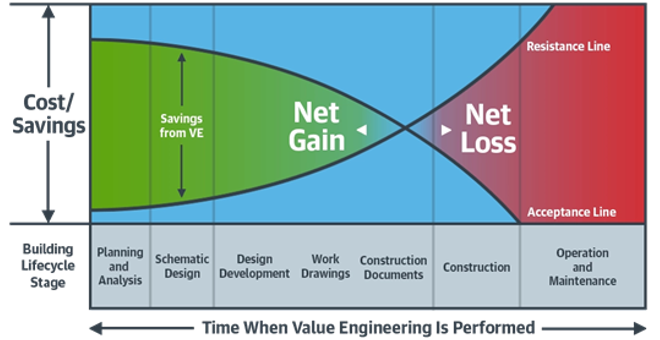
(Source: www.gordian.com)
Figure 4: Potential savings from value engineering
There is no “right” or “wrong” time for conducting value engineering exercise; but the earlier the process is, the better. This is because planning and design are the two stages of the building lifecycle where value analysis creates the most meaningful impacts. If value engineering becomes rework or causes project delays, it is no longer beneficial to the project. Figure 4 shows when value engineering moves from presenting a financial gain to a financial loss. To bear in mind, however, value engineering exercise should be conducted in such a way that no “safety issue” to be compromised. Any changes that would otherwise result in a violation of building code or jeopardize the health and well-being of the building occupiers should be rejected immediately.